Det var siste torsdag før jul. Likevel ble vår lille gruppe fra forskningsprosjektet Globoil tatt vel imot av entusiastiske medarbeidere i den verdensledende offshoreleverandøren TechnipFMC på Kongsberg. Vi er nok ikke de eneste som har hatt følelsen av at vi forholdt oss til noe naturstridig når vi svingte av fra E18 ved Drammen med retning mot den norske fjellheimen, for å besøke en leverandør som ikke bare rettet seg mot oljeindustrien offshore, men som endog har sitt spesialområde Subsea - altså innretninger som brukes under vann. Opplevelsen var nok ekstra spesiell for vår brasilianske PhD-student Tercio Pinho Filho, som var ny i vinter-Norge. Det var gråvær og temperaturer så vidt over null nede ved Oslofjorden. I de skogkledde åsene som omkranser Kongsberg sto derimot trærne med full vinterdrakt.
Det kunne se ut som om det var julenissens hemmelige verksted vi var på vei til, men der lå altså vinterlige Kongsberg, den gamle gruvebyen som etter en krise tidlig på 1800-tallet ble stor våpenprodusent, men som nå står som et av verdens mest avanserte senter for høyteknologisk subseakompetanse. Vi ble møtt av Sigmund Smøttebråten som hadde ledet utviklingen av en ny såkalt Subsea Control modul (SCM) i TechnipFMC.
Ved oljefelt offshore foregår en stadig større andel av den industrielle prosessen som skal til for å produsere olje under vann. Etter fusjonen mellom det amerikansk eide FMC og det franskeide Technip tidlig i 2017, kan den svært så internasjonale oljeleverandørgiganten levere så å si alt slags utstyr som brukes under vann, fra juletrær, manifolder, boostere, rørledninger som forbinder de ulike installasjonene til fleksible produksjonsrør og såkalte navlestrenger eller umbilicals som inneholder alle ledningene hvor utstyret styres fra.
Juletreets hjerne
Et "juletre" er den svært så komplekse installasjonen som befinner seg rett over en oljebrønn. En SCM er selve hjernen i en undervannsinstallasjon offshore.
Frem til tidlig på 2000-tallet ble det produsert juletrær på Kongsberg. For den som ikke kjenner offshoretermer spesielt godt, styrker det assosiasjonene til julenissens verksted ytterligere. Men et juletre er altså den svært så komplekse installasjonen som befinner seg rett over en oljebrønn. Det er denne enheten som kontrollerer at produksjonen foregår som den skal. Hvis det skal gjennomføres nye boringer eller andre typer intervensjoner i brønnen må alt foregå igjennom denne enheten. Alle enheter i installasjonen må kunne fungere under det ekstreme trykk og ofte svært kalde temperaturer som gjør seg gjeldende på dypt vann. Deler av installasjonen må dessuten kunne motstå det enda kraftigere trykket som gjør seg gjeldende nede i brønnen.
TechnipFMC har på 2000-tallet flyttet mesteparten av konstruksjonen av avanserte juletrær til bruk i Nordsjøen og en del andre markeder til Skottland. I Rio de Janeiro, Tercios’ hjemby, finnes det en tilsvarende fabrikasjon for det store brasilianske offshoremarkedet. Men det mest høyteknologiske av alt, selve hjertet i et juletre, SCM’en, blir altså produsert på Kongsberg og eksportert derfra til en rekke av verdens offshoreregioner.
Besøket på Kongsberg var innledningen til en langt mer omfattende studie av TechnipFMC fra Globoil. Sammen med Smøttebråten ga Even Skriudalen og Sverre Tjøntveit, også de ledere i selskapets avdeling for undervannskontrollsystemer, oss en innsiktsfull introduksjon både i hvor avgjørende effektive kontrollsystemer er for oljeproduksjon under vann og hvilke utfordringer denne delen av markedet står overfor.
En SCM er selve hjernen i en undervannsinstallasjon offshore. Det er herfra alle data fra hva som skjer med brønnen registreres og det her herfra alle intervensjoner styres. Det betyr at en SCM må ha et maskineri som er koblet opp til de ulike enhetene som utgjør et juletre. På utsiden har en SCM til nå hatt en standardisert, sylinderlignende form. Selv om det er en kostbar operasjon, kan en SCM hentes opp fra et juletre for særskilt vedlikehold. Undervanns «juletrær» kan virke like i formen for lekfolk. De er gjerne farget gule. Med alle sine ventiler får en like fullt umiddelbart inntrykk at dette er avansert industrivare. Siden hvert enkelt oljefelt er forskjellig dreier det seg i liten grad om hyllevare. Det betyr at hver enkelt SCM, treets hjerne, på tilsvarende vis må ha en innmat som er tilpasset alle særegenhetene ved oljefeltet hvor treet opererer. I fabrikkhallen på Kongsberg kunne vi se hvordan hver enkelt SCM ble konstruert manuelt. Sammenkoblingen av ledninger var et delikat arbeid som krevde lang intern opplæring. Konsekvensene av en enkelt feilkobling eller en løs skrue kunne over tid ble svært kostbare. Derfor ble det også brukt store ressurser på å teste alle produkter for alle tenkelige belastninger for de ble erklært ferdige.

Men selv om juletrær og deres kontrollmekanismer sett med noen akademikeres øyne kunne fremstå så avansert som det er mulig å få det, dreier deg seg om et marked preget av intens konkurranse, hvor ingen ting står stille.
TechnipFMCs avdeling for produksjon av kontrollsystemer står midt oppe i mange av de samme motsetningsfulle dilemmaene som preger øvrige deler av offshorebransjen når det gjelder innovasjon og konkurranse.
«Collaboration», konkurranse og standarder
Juletrær med tilhørende kontrollsystemer var i likhet med mye annet ved offshoremarkedet offshore lenge en amerikansk spesialitet. Når det som en gang var Kongsberg Våpenfabrikk leverte sine første juletrær på 1970-tallet, var det basert på lisens fra selskapet Cameron som den gang var internasjonalt ledende på området. Til og begynne med var ikke det norske bidraget større enn at den endelige sammensettingen av deler foregikk her. Men med den tunge ingeniørkompetansen som befant seg i det industrielle miljøet på Kongsberg, tok det ikke lang tid før produktet ble videreutviklet i Norge. Da FMC tidlig på 1990-tallet kjøpte seg inn i det som på daværende tidspunkt var Siemens-eide Kongsberg Offshore, var det ikke bare for å få slippe til i det betydelige norske subseamarkedet, men også for få tilgang til et kompetent ingeniørmiljø. En lang EPC-kontrakt for utvikling av undervannsinstallasjoner for Statoil ble på mange måter et gjennombrudd for FMCs teknologiske kompetanse for undervannsteknologi, også internasjonalt. Den norske avdelingen av selskapet ble sentral i selskapets globale virksomhet.
Når Statoil satte ut en så stor andel av utvikling og produksjon av undervannsteknologi til FMC, var de en del av en trend for outsoursing eller devertikalisering som har preget oljeindustrien siden 1980-tallet. Oljeselskaper skulle konsentrere seg om den type kompetanse som var mest spesifikk når det gjaldt å finne og utvinne mest mulig olje og gass. Det økonomisk optimale var at utvikling, fabrikasjon og vedlikehold av ne installasjoner og nytt produksjonsutstyr ble levert av selskaper som kunne utnytte stordriftsfordeler ved å levere til mange oljeselskaper samtidig. FMCs kontrakt med Statoil på 1990-tallet var sterkt preget av det som på innovasjonsforskningsspråket omtales som «collaboration». Nye undervannsløsninger ble utviklet gjennom et tett samarbeid mellom leverandør og operatør. Kværner og ABB fikk tilsvarende kontrakter med henholdsvis Hydro og Saga.
FMCs kontrakt med Statoil på 1990-tallet var sterkt preget av det som på innovasjonsforskningsspråket omtales som «collaboration». Nye undervannsløsninger ble utviklet gjennom et tett samarbeid mellom leverandør og operatør.
Men sett fra oljeselskapenes ståsted var det problematisk å bli avhengig av teknologien utviklet av en enkelt leverandør. Parallelt med utformingen av lange EPC-kontrakter støttet derfor Statoil aktivt opp at det ble utviklet særegne teknologiske standarder for norsk oljevirksomhet. Med støtte fra myndigheten og sammen med andre oljeselskaper og store leverandørselskaper ble NORSOK-standarden etablert. Senere har norske oljeinteresser arbeidet for at NORSOK-standarder skal internasjonaliseres gjennom den internasjonale standarden ISO. Ideen var at hvilke som helst leverandør skulle kunne byttes ut med en annen. Oljeselskapene ville sørge for konkurranse for å holde prisene nede. På den annen side dreide dette seg om så avansert teknologi at det var umulig for en leverandør å utvikle den nødvendige kompetansen hvis ikke kontraktene hadde en viss størrelse og varighet. Resultatet var at man sto igjen med noen få hovedleverandører i hvert segment. I Norge var det opprinnelig FMC Kongsberg, Kværner og ABB. Senere har det som opprinnelig var ABB blitt en del av Vecto Grey og deretter General Electric’s offshoreavdeling (GE), mens det som opprinnelig var Kværner i dag går under navnet Aker Solution.
På 2000-tallet har TechnipFMC og Aker Solution dominert når det gjelder leveranser av juletrær på norsk sokkel. I Mexicogolfen i USA har FMC og OneSubsea dominert, mens alle tre, inkludert den fjerde store leverandøren GE, konkurrerer i Brasil og flere av de andre offshoremarkedene globalt.
Men mens standardisering kan være med på å sikre effektiv konkurranse, kan det samtidig bidra til å sementere teknologier. Det vil alltid finnes rom for forbedringer når det gjelder både hvordan utstyr konstrueres og detaljer ved utformingen av dette utstyret. En viktig grunn til å innføre standarder er som vi kjenner fra hverdagen at man skal sørge for at det blir lettere å bruke dingser om hverandre, at koblinger skal passe sammen. Dermed må standarder være ganske detaljerte. Men med for detaljerte standarder kan en leverandør fristes til å kun velge å konsentrere seg om å levere allerede utviklet teknologi så billig som mulig. Man kan dermed havne i en situasjon hvor verken oljeselskap som bestiller eller hovedleverandører har sterke incentiver for forandring. I en situasjon hvor oljeprisen går jevnt opp over en lengre periode, som i perioden fra ca. 2003 til 2014/15, kan begge parter trives vel i en slik situasjon. Med et konstant voksende marked vil hovedleverandører som TechnipFMC og Aker Solutions sikre seg relativt god betaling for produktet selskapene kjenner godt. Oljeselskapene på sin side hadde det travelt med å klargjøre nye oljefelt for produksjon.
Hemmelig innovasjonsgruppe og krise i industrien
Til tross for fristelsen for å tilpasse seg eksisterende teknologi opprettholdt TechnipFMC, akkurat som hovedkonkurrenten i Norge Aker Solutions, en viss F&U-virksomhet. Begge visste at på lang sikt risikerte de å falle av lasset hvis konkurrenten kom frem med nye banebrytende produkter. De var samtidig klar over at prosessen var lang fra en helt ny ide til at et produkt var sertifisert, bestilt av et velvillig oljeselskap og klart til installasjon.
Slike vurderinger lå bak da Smøttebråten fikk i oppdrag av ledelsen i TechnipFMC å sette sammen et team som fikk i oppdrag å komme opp med en helt ny og mer kompakt løsning for SCM-moduler til juletrær. Gruppen ble satt ned i mars 2014, altså i god tide før oljeprisfallet. Tiden fra effekten av oljeprisfallet slo til for alvor i 2015 ble vanskelig for alle store offshore-leverandører. Etterspørselen av den type undervannsutstyr FMC og Aker leverte ble omtrent halvert. For TechnipFMC på Kongsberg ble dette reflektert i at antall ansatte ble nesten halvert, fra i overkant av 2000 til rundt 1200 i dag.
Under slike omstendigheter kunne det naturligvis være fristende å stenge ned et prosjekt som kun kunne gi inntekter på svært lang sikt. Men med oljeprisfallet fulgte et sterkt fokus fra oljeselskapenes side på tiltak som kunne redusere kostnadene. Det ga en åpning for radikalt nye konsepter. Også den etablerte F&U-gruppen måtte korrigere innretningen noe, blant annet ved å forkaste en del svært radikale ideer. Men den fikk de nødvendige ressursene internt i selskapet for å fortsette arbeidet med produktet.
Med oljeprisfallet fulgte et sterkt fokus fra oljeselskapenes side på tiltak som kunne redusere kostnadene. Det ga en åpning for radikalt nye konsepter.
Mens F&U-gruppen arbeidet kom det dessuten inn en ny forutsetning som var spesiell for det norske markedet. Statoil og senere Equinor ga tydeligere og tydeligere signaler om at selskapet ønsket en større grad av elektrifisering av driften offshore. Når Equinor signaliserte at selskapet vurderte bruk av vindmøller i tampen området eller elektriske kabler fra land til Johan Sverdrup feltet representerer ikke det i seg selv noe stort teknologiskille utover at små gasskraftverk og diesel aggregater på installasjoner og fartøy blir erstattet av andre kraftkilder. Equinor ønsket imidlertid i tillegg at mest mulig av operasjonene under vann skulle drives elektrisk.
De fleste som kjenner oljevirksomheten litt vet at oljeproduksjon offshore kan føre til betydelig utslipp av borevæske i havet, selv uten lekkasjer av olje eller gass. Færre kjenner nok til den utstrakte bruken av hydrauliske systemer for drift av undervannsinstallasjoner. Væskene i disse hydrauliske systemer kan inneholde kjemikalier som slippes ut i sjøen. Volumet av slike utslipp vil naturligvis være mindre enn borevæske. Equinor, som forbereder seg på en mulig intensifisert virksomhet i områder som det omstridte Lofoten, Vesterålen og Senja og langt nord i Barentshavet, er imidlertid opptatt av å komme opp med løsninger hvor selskapet kan vise til at utslippene til omgivelsene kan være tilnærmet null. Den nye kravet minner mye om vendingen som i første omgang fikk Statoil til å satse så sterkt på automatisert undervannsutstyr på 1990-tallet. Den gangen var det strenge norske reguleringer mot dykking på dypt vann som fikk den norske selskapene til å satse på ny teknologi. Reguleringen og oppfølgningen av de norske selskapene var sterkt medvirkende til at norsk teknologi ble ledende på undervannsområdet da Brasil og USA for alvor startet virksomhet på dypt vann få år senere.
Den nye produktet
Utviklingsprosessen som foregikk i TechnipFMC under krisen er så interessant at Globoil ønsker å studere den i detalj.
Men på Subsea Valley konferansen i Oslo høsten 2018 lettet selskapet på sløret. Selskapet hadde utviklet to separate, langt mindre og mer kompakte enheter som hadde alle funksjonaliteter som tidligere SCM-moduler. Litt forenklet var hjerne funksjonen og de hydrauliske styringsenhetene skilt fra hverandre. Det ville gi langt bedre fleksibilitet hivs oljeselskapene gjorde alvor av målet om å gå helelektrisk. Det var dermed lagt til rette for at den hydrauliske delen kunne skiftes ut med elektriske maskineri.
I utviklingen av prosjektet hadde innovasjonsteamet måtte forholde seg til alle de nevnte utfordringene, krav om kostnadsreduksjoner, tilpasning til det som ville bli fremtidens tekniske systemer, standarder som ga liten fleksibilitet for forandring og mye mer. Problemet med standarder gikk blant annet på at de relevante NORSOK- og ISO-standardene hadde spesifikasjoner for SCM-moduler i en hvis form og størrelse. De nye prosjektet brøt radikalt med standarden, men mente altså at det var mulig å lage et konsept som var billigere og bedre, med de samme funksjonene. Dermed var selskapet avhengig av en klarering fra operatørselskapene. Problemet med å gå til operatørene var at da økte faren for at den nye ideen lekket ut til konkurrentene. Dette ville særlig være et stort problem hvis prosjektet skulle knyttes opp mot et bestemt stort feltutbyggingsprosjekt. Da måtte all informasjon også deles med alle eiergrupper i lisensen.
Det som den gang fortsatt bare var FMC, valgte en mellomstrategi. I starten ble prosjektet holdt strengt hemmelig, både overfor oljeselskapene og blant andre ansatte internt i selskapet. I 2016 gikk selskapet til en stor leverandør og fikk aksept for at prosjektet ville kunne aksepteres fordi det hadde en funksjonalitet som var minst like god som standardene. Høsten 2018 ble altså konseptet også gjort kjent for konkurrentene. Det var imidlertid fortsatt langt igjen til at det nye konseptet var blitt til reelle store kommersielle leveranser og kanskje blir etablert som ny standard i industrien.
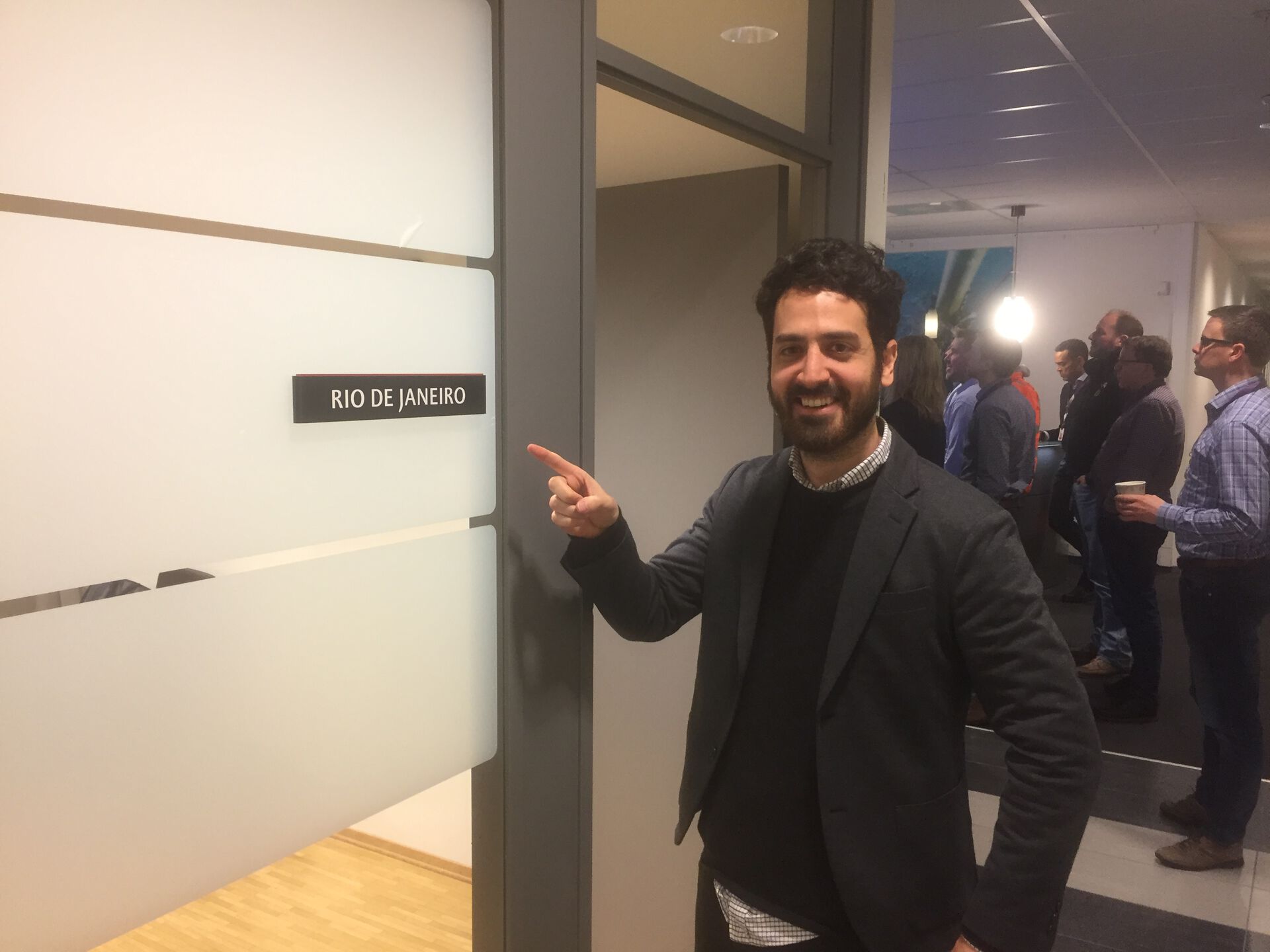
Vi fikk se kvalifikasjonsenhetene på fabrikkgulvet. Siden konkurrentene ganske sikkert arbeider med å produsere noe lignende har vi forståelse for at selskapet opererte med et strengt fotoforbud inne på fabrikken.
Mens vi hadde møte på grupperommet med navnet Rio de Janeiro var alle ansatte i gang med selskapets juleavslutning og årlige utmerkelser. Vi reiste hjem fra et vinterlig Kongsberg og følte oss litt klokere, men med mange nye spørsmål vi ville studere nærmere.